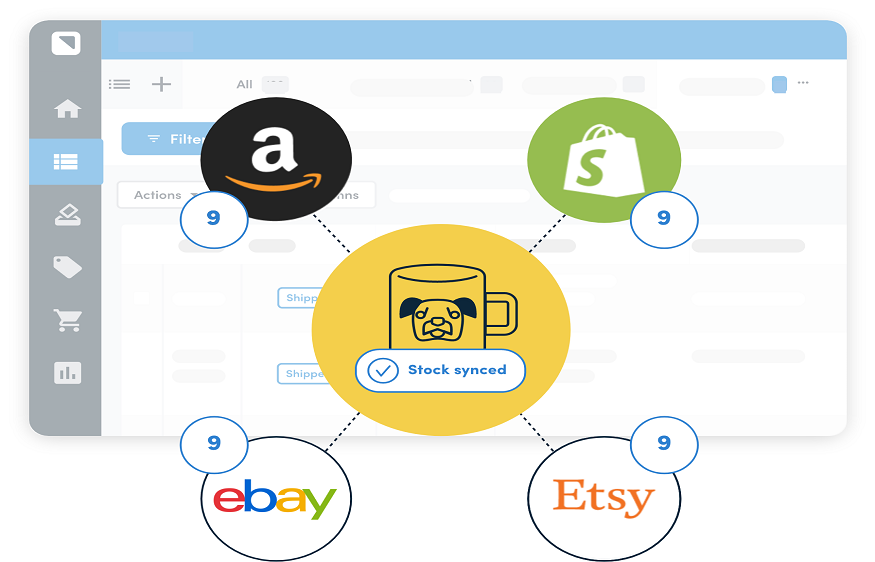
Any company engaged in the retail, direct-to-consumer (D2C), grocery, pharmaceutical, and wellness industries should keep a balanced inventory stock. Organizations involved in the production, for instance, might have raw materials, goods that are being manufactured, packaging supplies, and finished goods on hand. A company must have inventory planning software for all its divisions dealing with the goods they sell, manufacture, or purchase.
Inventory planning is a technique for determining the best time and amount to stock inventory so that the production is in line with the demand from customers. Planning for inventory has a variety of effects on a business. It impacts various aspects, including those that directly affect a company’s cash flow and revenue growth when it comes to companies that rely too much on quick turnovers of goods and materials. Every firm should find the best inventory forecasting software for themselves because inventory planning is a crucial component.
Businesses can profit from efficient inventory planning and successfully meet customer demand. Inventory should be stocked at the ideal amount to avoid overstocking and lower the expense of storing, cooling, and heating the extra product. To prevent expensive last-minute supplier purchases and acquire goods at a lower cost, businesses can estimate demand and plan inventories accordingly.
How to Optimize Inventory Planning?
An efficient inventory planning software is crucial for a profitable business. The most crucial factor for a retail firm is to have high-selling items stacked up in the appropriate places to satisfy customer demand at the ideal moment. As your firm grows, you must monitor and manage different sales channels to meet customer expectations across all distribution channels. It is a difficult operation, and you must keep track of the goods at all times, including in warehouses and dark locations. Inventory planning software is necessary because manually keeping inventory track is difficult.
Inventory planning software determines the best time to place replenishment orders and the ideal inventory levels to match production and sales capacity. It aids in precise demand forecasting, a seamless and effective supply chain, and increased customer satisfaction. This technology ensures that all shipments can be easily tracked and monitored in real time. Businesses should adopt the most recent and updated inventory planning software to streamline services and maintain continual communication with their clients.
By implementing effective inventory planning software, quick-commerce companies can avoid situations that result in losses. Additionally, it improves sales and customer experience. Modern software uses AI and ML algorithms to examine historical sales data and offer companies data-driven insights that help them save time and money while optimizing pricing and product allocations. Retailers can adapt to changing consumer demand with reliable inventory planning software. It helps to decrease overstocking and stockouts, optimize inventory placements, boost cash flow and profits, expedite order processing, reduce lead times, and place replenishment orders.
Assessing Optimal Service Levels
Each retail business must control its inventory costs. The most typical approach is to set the desired inventory level and then continuously purchase more of a product as it approaches running low on stock. By overstocking some products, this practice has the tendency to tie up working capital if it isn’t done well. Service level optimization can aid in resolving this issue. To assure profits, managers should identify the SKUs that generate most of the sales revenue and maintain good service standards. This will ensure they never lose out on sales opportunities for products in great demand. They can achieve this by classifying the entire SKU group with ABC classifications to ensure sufficient service levels.
Supplier Fill Rate
The percentage of orders a supplier has typically filled is known as the supplier fill level. Utilizing past purchase and GRN data at the SKU-vendor level, fill rate modifies safety buffers. When determining order suggestions in Kronoscope, supplier lead time variability can be considered by utilizing the 95th percentile of supplier lead time.
Replenishment lead times
The lead time from a higher-level node to a lower-level node is known as the replenishment lead time. Retail businesses should prioritize cutting lead times as much as they can. Low inventory or days on hand are essential for a resilient and responsive supply chain. Inventory is necessary for demand unpredictability, lead time variations, and service levels.
Calculating Dynamic Safety Levels
To prevent waste, retail organizations must maintain a high inventory turnover ratio, necessitating more careful planning of their safety stock. By evaluating lead times, fill rates, shelf life, current inventory levels, open orders, and current safety stock levels, they must develop a dynamic safety levels plan. Dynamic safety levels should be assigned based on the service level and demand variability. For high-selling products with high demand variability, high dynamic safety standards should be maintained. A very effective technique to prevent overstocking inventory and service levels is to optimize service levels.
Purpose of Inventory Planning Software for Quick Commerce Businesses
An eCommerce organization gets its shape and structure through systematic planning. Without reliable inventory planning software, a company would be vulnerable to understocking, overselling, and delayed order fulfillment, negatively affecting customer experience. Organizations can benefit from improved customer experience and the following advantages with systematic inventory planning:
- Enhanced Cash Flow – When a lot of slow-moving products are stacked up in a warehouse, eCommerce companies are forced to reduce the price of the products to prevent waste and free up capital stored in products with little demand for investing in more lucrative products and products that sell more.
- Expanding eCommerce – Online purchases are growing yearly as more people make more purchases. E-commerce companies must scale their inventory through structural and agile planning to meet this increased demand.
- Improved Customer Experience – Increased customer expectations mark the modern, current era. They expect not to have to wait a long time to fulfill their requests. Before buying something and placing their trust in a firm, customers read online reviews. When consumers have a bad shopping experience, they often write bad reviews. It costs a lot of money to respond to bad reviews. Thus, preventing them from arising in the first place is preferable. By offering the appropriate products, speeding up order processing, and eliminating mistakes, effective inventory planning helps meet customer expectations. These errors can damage a company’s reputation and cost it time and money.
About Fountain9
Quick-commerce businesses can get help from Fountain9 with precise demand forecasting. All internal and external factors are taken into account by their AI-powered inventory planning software, Kronoscope, to forecast demand and plan inventory appropriately. Businesses may maintain their stock at the ideal level and meet customer expectations at the appropriate moment by using Kronoscope.
Elaborate these points please and replace :
>> Supplier scoring/selection
>> Dynamic Safety stocks
>> store capacity optimization
>> Lead time considerations